Flexible Coupling
A flexible coupling is used to connect two shafts, end-to-end in the same line, for two main purposes. The first purpose is to transmit power that is torque from one shaft to another, thereby causing both to rotate in unison, at the same RPM. The second purpose is to compensate for small amounts of misalignment and random movement between the two shafts.
Flexible couplings are made of elastic materials, like rubber, or have various other configurations. During rotation, flexible couplings can accommodate misalignment and motion.
How flexible coupling operates?
It is a known fact that in any direct mechanical drive system, there is
the need to couple the variety of driven elements that are included. The
majority of drive elements which include gear reducers, lead screws, and
a host of other components, are driven by shafting. The shafting is
supported by multiple bearings. This allows the shafting to be held
extremely straight and rigid while rotating which at the same time avoid
any kind of possible balancing and support problems. Because of this
rigid support, it practically becomes impossible to avoid slight
misalignments between a driving and driven shaft when they are
connected.
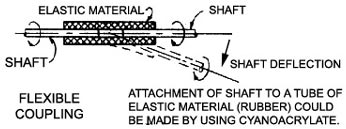
The simple and most common solution to the problem of shaft
misalignment is using a flexible coupling to absorb lateral, angular,
and axial restoring forces, while maintaining some rigidity or fixed
position in rotation. The degree to which this torsional rigidity is
applied varies from one application to another. The basic function of
flexible coupling is to join two pieces of rotating equipment while
permitting some degree of misalignment or end movement or both.
Materials used:
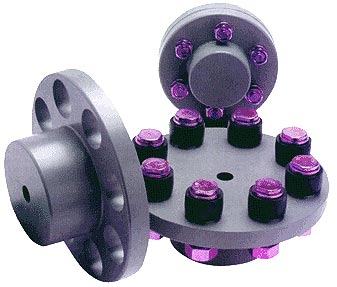
Various materials are used to make flexible couplings like as follows:
- Brass
- Aluminum
- Cast Iron
- Stainless Steel
- Carbon Steel
- Rubber etc.
Types of flexible coupling:
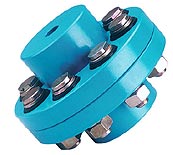
There
are three basic types of flexible couplings. They are as follows:
- Mechanically Flexible Coupling: The mechanical flexible
coupling generally obtain their flexibility from loose-fitting parts
or rolling or sliding of mating parts or from both.
- Metallic Element Coupling: The metallic flexible
couplings obtain their flexibility from the flexing of thin
metallic, disc or diaphragms.
- Elastomeric Element Coupling: The elastomeric element
flexible coupling obtain their flexibility from stretching or
compressing a resilient material like for example rubber or plastic.
Buying tips When searching for flexible couplings, some
mechanical properties that are to be considered are as follows:
- Rated torque: This is the maximum service torque for
which coupling is rated.
- Rated speed: This is the maximum rated rotational
speed of coupling.
- Stiffness: This is expressed in torque per unit
angular deformation.
- Backlash: This is the rotational position loss in a
direction change.
- Performance:
- The most common flexible coupling recommended for
general-purpose equipment alignment should be one within
0.001 inch/inch of separation between flex points.
- For high-speed applications like over 3600 rpm, alignment
should be within 0.0005 inch/inch of separation between flex
points.
- For general-purpose equipment and couplings, the
alignment should be “zero” align statically.
- When alignment is carefully done initially, there should
be enough capacity left in the flexible coupling to handle
more misalignment during operation.
|
Functions of flexible coupling:
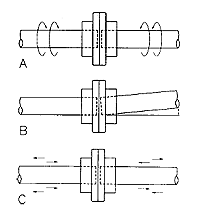
There
are three basic functions of a flexible coupling. They are as follows:
- Transmit power: Flexible couplings are used to transmit
mechanical power from one machine to another. The mechanical power
is in the form of torque at some speed, or work per unit of time, In
general, the power lost by a flexible coupling is small.
- Accommodate misalignment: There are two types of
misalignment. They are shaft misalignment and coupling misalignment.
Both the misalignments are accommodated through flexible coupling.
- Compensate for end movement: Most flexible couplings are
designed in such a way that they can accommodate axial movement of
the connected equipment or shaft ends.
Applications of flexible couplings:
- Off-highway vehicles
- Agricultural machinery
- Marine propulsion
- Rail traction
- Pump sets etc.
Conclusion:
The flexible couplings are available from a large number of different
manufacturers, each of which designed them with specific applications in
mind. Ideal linkage can be achieved for any motion system with proper
selection of the right flexible coupling for any application.
The points mentioned below will be a guide for the buyers: